|
Mixer-disperser DRS ® is used for getting stable mixtures of fuels, heavy fuels quality increasing with dispersing asphalt-resin substances, getting water and fuels emulsions, increasing quality of fuel additives.
Several developments have obtained patents of Latvia, Russia, and Germany.
|
|
|
Mixer-disperser DRS (hereafter referred as disperser) is used for getting stable mixtures of fuels, heavy fuels quality increasing after dispersing asphalt-resin substances, getting water and fuels emulsions, increasing quality of fuel additives; it may oil waste prepare for utilization and make emulsions for metal cutting machines. Disperser is used in fuel preparation systems of plants' boilers, vessel's boilers, internal combustion engines, gas-turbine facilities.
The economical effect is 1-5% of fuel incinerated by power facility. Besides fuel economy, mixer-dispersed provides environmental effect, because it decreases chemical incompleteness of combustion and provides a possibility to use watery oil waste that usually are transported to a dump.
Presently it is widely used in processing "cargo waters" at plants' boiler rooms, watery oil products utilization at vessels' boilers and emulsoles at ferroconcrete constructions plants boiler houses, for stabilization of lube-cool liquids and further processing of waste, in fuels mixtures preparation for vessels diesels.
The utilization of oil waste is performed by adding them to basic fuel, further processing of mixture by mixer-disperser and incinerating this mixture as a fuel.
Disperser DRF, made of stainless steel, is used in food industry (for instance, in preparing juices), also in medicine in emulsions and suspensions preparation.
The company's innovation department has launched a new line of dispersers used to process explosive petroleum products.
This type of disperser is made of stainless steel with explosion-proof electric motors
In these homogenizers, the productivity (10 cubic meters per hour) and the pumping effect (outlet pressure — 2 bar) were preserved, as in the ones we previously produced, but the flow part was improved.
This allows you to break up long chains of hydrocarbons with breaking chemical bonds and the formation of free radicals.
At the same time, the absolute surface of liquid fuel increases, which leads to a significant increase in the rate of its evaporation and combustion.
This, in turn, entails a reduction in emissions and a softer engine operation.
In addition to use on ships, diesel power plants, dispersers can also be used in boiler plants, as well as in the chemical industry, including for accelerating chemical reactions in technological processes.
In power plants, dispersers can also be used to prepare water-fuel emulsions
Picture 1 shows the disperser in an explosion-proof design, and picture 2 shows a conventional disperser.
„CORVUS Company” provides selling, installation, staff training, warranty services.
|
|
Pict. 1
|
Pict. 2
|
|
|
Mixer-disperser (fuel)
|
Mixer-disperser (food)
|
SPECIFICATION
Capacity, m3/h 10
Produced pressure, MPa 0.2
Power kW 5.5
Rotation frequency, rpm 2900
Electric engine powering:
Voltage, V 380/220
Current frequency, Hz 50
Safety coefficient 0.95
Measurements, mm
Length 525
Width 280
Height 300
Mass, kg 65
|
|
Disperser works as follows: Fuel or its mixture with water get to a disperser with a drift through two input holes from two different levels (see picture 2): from the lower point of cistern and from the fuel input point to boiler. Rotor, rotated with electrical actuator, with his working disks intensively mixes the fuel or fuel and water mixture and transfers it from the small rotor's disk to an impeller, throwing ready emulsion through disperser's output hole in the cistern. During the mixing process asphalt-resin particles of fuel and water are emulsified with disks and cavitations processes. As a result, it produces highly dispersed stable emulsion.
After cistern's content double processing in disperser, the fuel is ready for incineration in boilers.
The mixer-disperser is especially effective in incineration of heavy fuel oils of high viscosity, containing a big amount of asphalt-resin particles. After heavy fuel oil is incinerated, asphalt-resin particles do not burn (incomplete chemical incineration), that is seen by a dark smoke coming out of the chimney of boiler house. Such heavy fuel oils need to prepare a homogenous water and oil emulsion, well performed by mixes-disperser.
The process of water-oil emulsion incineration has substantial differences from incinerating pure heavy oil. In water-heavy oil emulsion around water drop there are asphalt-resin substances, as natural surface-active substances. Because water and heavy oil boiling temperatures are different (at normal conditions water's boiling point is 100оС, and heavy oil – more than 300оС), during heating in hot environment of boiler water turns to steam before the heavy oil.
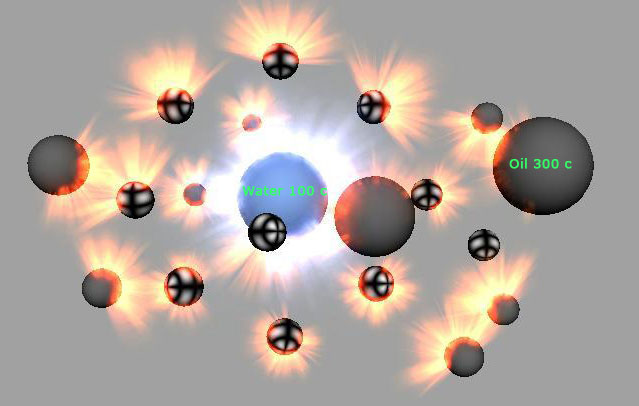
Pic. 3
As a result, when pressure of water steams is more than the surface heavy oil layer tension (due to greater flexibility of water steams and increase of volume more than several hundred times after water turns to steam, water drop vaporizes very actively), so called "micro-explosion" happens (see picture 3), heavy oil particles scatter around, oil steams vaporize intensively and additionally being mixed with oxygen in air, improving emulsification. After that the fuel incinerates completely and so being saved.
Maximum economy after incineration of water-heavy oil emulsion prepared with a mixer-disperser is with water content ~10%; after increasing water content to 18-20% the fuel consumption does not decrease (so fuel consumption economy is compensated with its consumption for water vaporization), and with water content above 20% the fuel consumption increases.
Mixer-disperser allows receiving a stable homogenous water-heavy oil emulsion, ensuring fuel consumption economy due to complete heavy oil incineration.
The same effect is seen during emulsion preparation of basic boiler fuel (heavy oil) and watery oil waste.